Together, five key principles work together to help companies meet the main goal of lean inventory management: increased efficiency.
The basis of these principles comes from a 1996 book by James Womack and Dan Jones, founders of the Lean Enterprise Institute and the U.K. Lean Enterprise Academy. In Lean Thinking: Banish Waste and Create Wealth in Your Corporation, the authors laid out the main principles of lean manufacturing.
For the purposes of lean inventory, Womack’s and Jones’ concept of the “value stream” is often expressed as “responsiveness.” The value stream looks at the entire product lifecycle, from raw material to eventual disposal. Responsiveness is a narrower concept, concerned with staying nimble enough to pivot inventory to meet changes in demand or supply.
Related: What Is Lean Inventory Management & How Does it Work?
1. Value:
Under the five Lean principles, value refers to what customers want and will pay for. From an inventory perspective, businesses need to factor in customer demand when determining how much and what inventory to stock. Determining this is a function of demand planning, a cross-functional process that helps companies give customers what they want — thus minimizing excess inventory and dead stock.
2. Flow:
To apply lean inventory practices, companies must understand how inventory flows within the organization. A solid materials requirements planning (MRP) practice asks three questions, with responses dictating flow: What is needed? How much is needed? When is it needed by? The answers need to drive production schedules.
3. Pull:
A pull-based system is intrinsic to JIT inventory management, where products are created only when, and in the quantities, required. Pull follows naturally from the flow process and contrasts with a more demand-centric push-based system, which relies heavily on historical sales data to determine production levels.
4. Responsiveness:
The flexibility to adapt to change helps head off increased carrying costs and out-of-stock situations. Inventory management best practices including ABC analysis, demand forecasting, and Economic Order Quantity (EOQ) aid responsiveness.
5. Perfection:
Striving for perfection encapsulates the lean philosophy — whether we’re talking manufacturing, inventory management, or any other process. Continuous improvements to improve quality and eliminate waste and inefficiency move companies closer to the ideal.
You Should Also Read:
How Does Information Technology Affect Supply Chain Management?
Logistics 4.0 and Smart Supply Chain Management
What is Cold Chain Management?
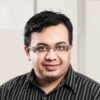
Danish Mairaj is a medical device expert with a strong focus on regulatory and quality compliance. He has been involved in managing clinical trial infrastructure including supplies and logistics. He has over 15 years of experience in the MedTech and Pharmaceutical industry. He is a certified Product Owner, Scrum Master, and Project Management Professional PMP. He studied Biomedical Engineering in Germany and MedTech Regulatory & Quality in Galway, Ireland. He contributes articles to the BRASI newsletter.
- Danish Mairaj#molongui-disabled-link