Collaboration in the supply chain refers to the practice of different entities working together to achieve common goals and improve overall efficiency and effectiveness. Whether it’s a collaboration between suppliers, manufacturers, distributors, retailers, or other stakeholders, there are several benefits that can be realized through collaborative efforts.
Advantages of Collaboration in the Supply Chain
Enhanced Visibility and Transparency
Collaboration allows for better visibility and transparency across the supply chain. When partners share information and insights, it becomes easier to track inventory, monitor production processes, and gain real-time visibility into demand fluctuations. This shared visibility enables proactive decision-making, reduces uncertainty, and improves overall operational efficiency.
Improved Forecasting and Planning
By collaborating closely, supply chain partners can exchange data and information related to demand forecasts, sales forecasts, and inventory levels. This enables more accurate demand planning and forecasting, leading to better inventory management and reduced stockouts or overstock situations. Enhanced planning capabilities also allow for optimized production scheduling, reduced lead times, and improved customer service levels.
Cost Reduction
Collaborative supply chain efforts can result in significant cost savings. By sharing resources, pooling transportation, or jointly procuring raw materials, companies can achieve economies of scale and negotiate better prices with suppliers. Collaboration also reduces redundant activities, eliminates bottlenecks, and minimizes inventory holding costs, resulting in overall cost reductions across the supply chain.
Increased Flexibility and Agility
In today’s dynamic business environment, supply chain partners must be agile and responsive to changing market conditions. Collaborative relationships foster flexibility by enabling quick adjustments to production schedules, inventory levels, and distribution plans. When partners share information and work together closely, they can respond more effectively to disruptions, such as supply chain disruptions or changing customer demands.
Innovation and Continuous Improvement
Collaboration fosters an environment of innovation and continuous improvement. When vendors collaborate, they can share knowledge, insights, and best practices, leading to the development of new and improved processes, products, and services. Collaborative efforts can also facilitate joint problem-solving, enabling partners to address challenges and implement innovative solutions more effectively.
Risk Mitigation
Collaboration in the supply chain allows for better risk mitigation. By sharing information about potential risks and vulnerabilities, partners can collectively identify and assess risks and develop strategies to minimize their impact. Collaborative relationships also enable the development of contingency plans, alternative sourcing options, and shared risk management practices, ensuring greater resilience and robustness in the supply chain.
Enhanced Customer Satisfaction
Collaboration in the supply chain ultimately benefits the end customer. By improving visibility, reducing lead times, and enhancing overall operational efficiency, companies can provide better service to their customers. Collaborative efforts can enable faster order fulfillment, accurate delivery tracking, and improved responsiveness to customer inquiries or issues, leading to higher customer satisfaction levels.
Conclusion
Overall, collaboration in the supply chain offers numerous benefits, including enhanced visibility, improved forecasting and planning, cost reduction, increased flexibility, innovation, risk mitigation, and improved customer satisfaction. By working together, supply chain partners can create a more efficient, resilient, and customer-centric supply chain ecosystem.
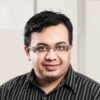
Danish Mairaj is a medical device expert with a strong focus on regulatory and quality compliance. He has been involved in managing clinical trial infrastructure including supplies and logistics. He has over 15 years of experience in the MedTech and Pharmaceutical industry. He is a certified Product Owner, Scrum Master, and Project Management Professional PMP. He studied Biomedical Engineering in Germany and MedTech Regulatory & Quality in Galway, Ireland. He contributes articles to the BRASI newsletter.
- Danish Mairaj#molongui-disabled-link