Lean methodology involves maximizing value and minimizing waste, making understanding its eight wastes crucial for reducing inefficiencies in any process. Overproduction, underutilized talent, and other significant waste factors can drain resources and reduce productivity if left unaddressed.
But how do you identify and resolve these inefficiencies?
In this blog, we’ll break down each waste and provide actionable strategies to tackle them effectively. Whether you work in manufacturing, supply chain, or logistics, these insights will help streamline operations and foster a culture of continuous improvement.
What Are the 8 Wastes of Lean?
The 8 wastes of Lean are common inefficiencies that disrupt workflows and hinder success. They include Transportation, Inventory, Motion, Waiting, Overproduction, Over processing, Defects, and Skills. Each of these represents an area where time, money, and resources are wasted. Let’s explore each waste and practical ways to address them.
Understanding TIMWOODS: The 8 Wastes Explained
1. Transportation
Transportation waste is the unnecessary movement of materials, goods, or tools that adds no value to the customer. For example, raw materials might be moved through multiple stages across long distances before processing begins. This not only wastes time but also increases the risk of damage and delays. Addressing this involves reorganizing workspace layouts and streamlining workflows. Value stream mapping is a particularly effective tool for identifying and minimizing excess transportation in processes.
2. Inventory
Excess inventory is like money sitting idle. It ties up capital, takes up storage space, and can even lead to spoilage or obsolescence in industries like food or technology. Businesses can address inventory waste by implementing systems like Just-In-Time (JIT), which focuses on ordering and receiving materials only when needed. Demand forecasting tools also help ensure that stock levels align with actual customer requirements, avoiding overstocking or understocking.
3. Motion
Wasted motion occurs when workers or machines move unnecessarily, such as employees frequently walking long distances to retrieve tools or documents. These small inefficiencies add up over time, impacting overall productivity. Organizing workspaces to place tools and materials within easy reach can significantly reduce wasted motion. Additionally, ergonomic solutions improve efficiency by making tasks less physically demanding and time-consuming.
4. Waiting
Waiting is one of the most visible forms of waste. Whether it’s a machine idling during a breakdown or employees waiting for approvals, delays disrupt the workflow. Addressing this waste involves balancing workloads across teams and ensuring that equipment and resources are well-maintained and readily available. Proactive scheduling and cross-training employees to perform multiple tasks can also help minimize downtime.
5. Overproduction
Producing more than what is needed is a common issue that creates ripple effects of waste, including excess inventory and unnecessary costs. For example, a factory producing extra units to “be safe” might end up with unsellable goods. This can be mitigated by aligning production schedules closely with actual demand. Standardizing production processes to create batches that meet customer needs, rather than exceeding them, is a proven strategy to combat overproduction.
6. Overprocessing
Sometimes businesses overdo things—adding unnecessary steps or features that don’t add value for the customer. A classic example is excessive packaging. Simplifying processes by focusing on what the customer truly values is key to eliminating overprocessing. Lean tools like Six Sigma can help streamline workflows and eliminate redundant steps that consume resources without improving outcomes.
7. Defects
Mistakes or flaws in products can result in expensive rework or even product disposal, wasting valuable time and resources. A good and strong quality control must be taken by implementing routine inspections, and operational standards must also be clear. Along with it, train employees to hunt out and resolve problems in time at production, so they can be dealt with at a more manageable stage and satisfy the customer.
8. Skills
The most overlooked waste is underutilizing the skills and talents of employees. This happens when workers are given tasks below their capability or aren’t encouraged to contribute ideas. Creating opportunities for training, development, and involvement in decision-making can unlock the full potential of your team. Employees who feel valued are more likely to take ownership of their work and identify ways to improve processes.
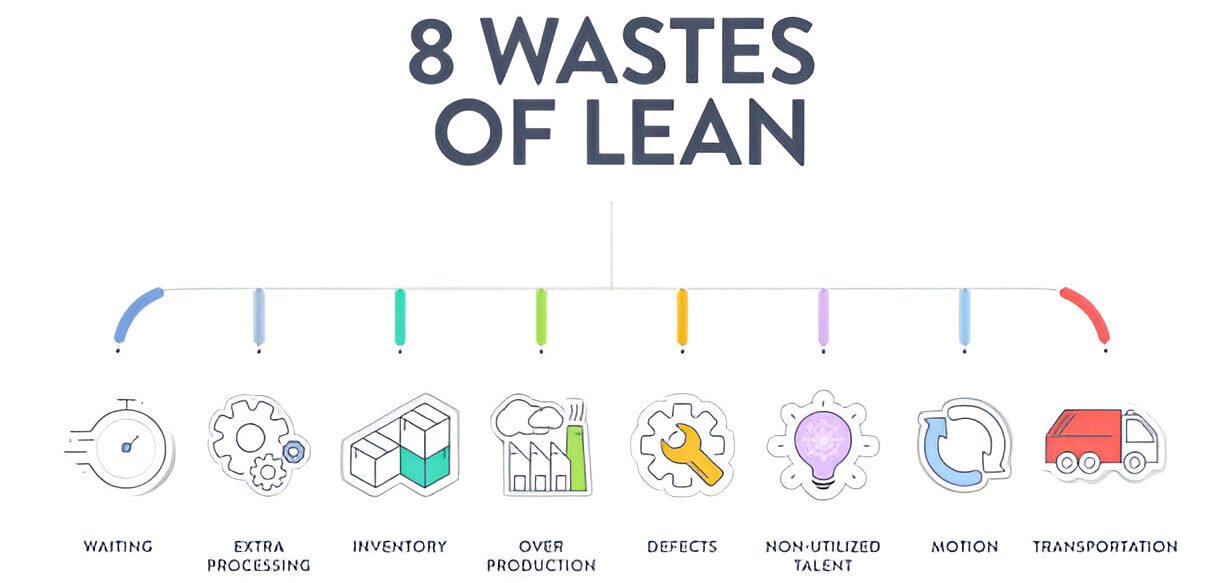
8 Wastes of Lean Examples
Examples make these concepts come alive. Consider these scenarios:
- Transportation: A warehouse unnecessarily moves products across multiple stations.
- Inventory: A retailer overorders seasonal stock, leading to surplus.
- Motion: Employees walk across the shop floor multiple times to fetch tools.
- Waiting: A production line halts because materials haven’t arrived on time.
- Overproduction: A bakery produces twice as many loaves as it can sell.
- Overprocessing: A product undergoes extra polishing that customers neither notice nor need.
- Defects: A smartphone manufacturer recalls units due to faulty software.
- Skills: A skilled analyst is stuck performing repetitive data entry tasks.
8 Types of Waste in Lean Six Sigma
When combined with Lean Six Sigma, waste elimination becomes even more powerful. Six Sigma tools like DMAIC (Define, Measure, Analyze, Improve, Control) provide a structured approach to identifying and addressing waste. This methodology not only removes inefficiencies but ensures that processes stay optimized over time.
Timwoods and Its Application
TIMWOODS serves as a helpful checklist to spot waste in daily operations. By teaching teams to recognize and act on these inefficiencies, businesses can create a proactive culture of continuous improvement. Workshops and regular reviews ensure that TIMWOODS isn’t just a concept but a practical tool for driving change.
Practical Strategies to Eliminate the 8 Wastes
Combining Lean principles with actionable strategies can yield remarkable results:
- Value Stream Mapping: Use this tool to visualize your processes and identify problem areas.
- Standard Work: Establish consistent methods to reduce variability.
- Kaizen: With small, regular changes Kaizen fosters a culture of continuous improvement.
- 5S Methodology: Sort, Set in Order, Shine, Standardize and Sustain. This method organizes workspaces for maximum efficiency.
- Automation: Leverage technology to predict demand, monitor inventory, and streamline processes.
- Employee Engagement: Encourage teams to share their insights and ideas for improving workflows.
Why Eliminating Waste Matters
Waste elimination isn’t just about cutting costs; it’s about creating a better business. Streamlined operations lead to faster delivery times, higher-quality products, and happier employees. Customers benefit too as they get what they need, when they need it, without paying for inefficiencies.
Final Thoughts
Mastering the art of eliminating the 8 wastes of lean is more than just a strategy—it’s a mindset. By identifying inefficiencies and implementing practical solutions, organizations can achieve a smoother workflow, higher productivity, and greater customer satisfaction. The journey may demand persistence, but the results are worth it: a leaner, more agile operation poised for sustainable success. Embrace these strategies today, and take a decisive step toward building a waste-free, value-driven future for your business.
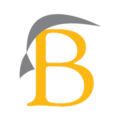
We have been offering extensive and well-planned pieces of training in the field of economics, supply chain, and operations management. Our core purpose is to help industry professionals and businesses to succeed in an ever-evolving competency in the jobs market. Our cutting-edge training methods and up-to-date knowledge aligned with the latest industry trends and demands put our candidates in the lead amongst other job seekers and competitors in the market.
- BRASI Editorial Team#molongui-disabled-linkSeptember 3, 2024
- BRASI Editorial Team#molongui-disabled-linkOctober 8, 2024
- BRASI Editorial Team#molongui-disabled-linkNovember 19, 2024